top of page

Die Casting Lubricants
DIE CASTING
LUBRICANTS
DILUCO
Our Diluco family of high-performance, ready-to-use die lubricants are formulated to promote cleaner dies while increasing productivity for for zinc, magnesium or aluminum die casting applications. The blend of chemically-balanced lubricants provide superior lubrication, low build up, and water-based or oil base options.
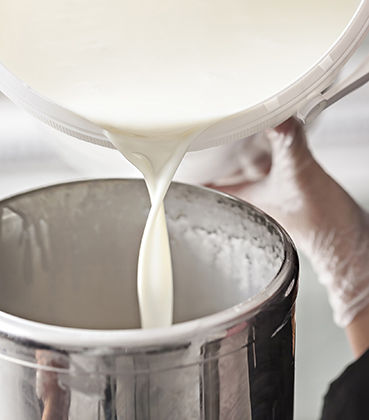
Plunger Lube
PLUNGER
LUBRICANTS
SUPERIOR TIP & SLEEVE LUBRICATION
Our easy-to-apply Plunger lubrication family of products include liquids, graphitic beads and non-graphitic beads. Each product is suitable for your die casting application, whether for aluminium, zinc or magnesium. Our unique lubricants work under extreme pressure and high temperatures while providing extended life of tip and sleeve.
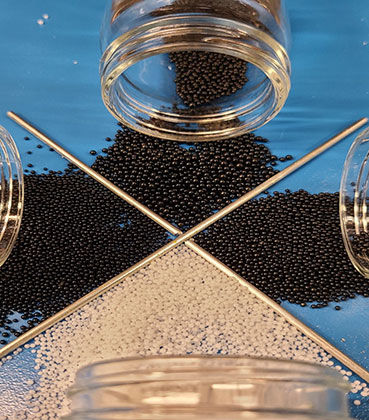
Auxiliary Products
AUXILIARY
PRODUCTS
DIE CASTING OPERATIONS
We want to become your one-stop resource for your die casting operations. Through the years, we’ve expanded our available products to ensure our customers can easily access the highest quality products for every stage in their operations, including:
​
-
Ladle Coatings
-
Quenches
-
Cleaners
-
Anti-Seize Products
-
Rust Prevention Products
-
Trim Lubricants
-
Equipment, Accessories & More

HYDRAULIC
FLUIDS
GRIFLUBE
The Griflube family of hydraulic oils offers biodegradable, Factory Mutual approved, and high-temperature products to meet all industrial lubrication needs. Utilizing close partnerships with ILMA and STLE, we can provide some of the most cutting-edge lubrication on the market.

Hydraulic Fluids
METALWORKING
FLUIDS
MACHINING APPLICATIONS
From cutting fluids to cleaners, access our high-quality metalworking fluid products for your machining applications. H&G offers many cutting edge metal removal chemistries, metal forming lubricants, industrial cleaners and machine lubrication products.
We work with our customers on their most critical issues, such as troubleshooting solutions, environmental issues and lubrication engineering planning. We are committed to providing practical solutions to our customers' manufacturing challenges.

Metalworking Fluids
Permanent Mold Coatings
PERMANENT
MOLD COATINGS
CONCOTE
Concote permanent mold coatings are developed to provide excellent surface finish and prevent premature die failure for low pressure die casting. It has a dilutable formula with special refractories, binders, wetting agents and preservatives. It is easily applied and, once dried, leaves a continuous thin film between the surface of the die and the casting.

bottom of page