Die Temperature And Surface Die Casting Defects
- Hill and Griffith
- Dec 5, 2018
- 4 min read
NADCA EC-515 Die Casting Defects Course Review, Basics for controlling die casting defects - By Dr. Steve Midson
The die temperature’s effect on surface defects and the die temperature operating window will be discussed next
A low die temperature affects surface defects by cooling the fluid metal stream and increasing the percent of solidified metal in the metal stream
If the percent of solidified metal is high, then it becomes stiff and solid and does not knit together well; And the flow forms "wrinkles", or cold flow
A cold die can be compensated for by having a shorter fill time - this means a higher plunger speed
In other words, we can exchange plunger speed for die temperature.
Measuring die temperature should be done on every job - most don’t do it enough, but it is required to really minimize surface defects
In general, measuring can be done three ways: – Hand held probe – Thermocouple in the die – Infra red device
Each has advantages and disadvantages: Hand held probe: accurate, but must stop the machine; Thermocouple in die: continuous, but does not measure surface temperature; Infra red: easy, but not as accurate

The operator can control die temperature with the following controls: Die spray; Water/oil flow rates; Cycle time
The engineer can change the design and affect how much difference some of these make, but the operator often controls the actual use of all of them. Thus the operating temperature of the die is often controlled directly by the operator and this die temperature control is probably the most important activity of the operator on the floor. We will review these in sequence
Die spray is lubricant mixed with water, it is mostly water
The water controls the temperature, not the die spray itself
The spray cools the die quickly because of the large amount of heat quickly pulled out of the die as the water in the spray boils away
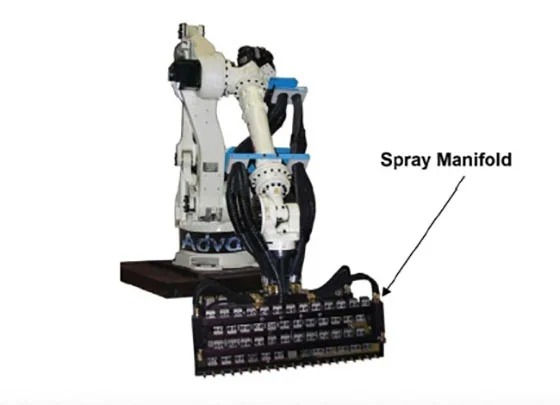
Some techniques include: spray in 2-3 second increments with careful adjustment of the spray pattern - spray the areas that need cooling, not just where the casting might stick - automatic sprayers with a set manifold for each job are a good way to keep spray to a minimum
Keep spray equipment in good shape, the most important factor is consistency
Document pressures, nozzles sizes, flow adjustments, and spray times in detail -undocumented changes should not be allowed (changes should not be stopped, just documented)
Factors in the spray actions that are very important in controlling die temperature: Length of time of spray; Spray nozzle adjustment, or spray pattern; Distance from nozzle to the die; Balance between air pressure and lube pressure (drop size and velocity); Minimize over spraying; Document everything - spray time, pressures, spray location, mixtures, etc...; Be consistent

With water, flow rate is usually more important than the temperature of the fluid. A small difference in flow rate will do more than a large difference in temperature
Measuring flow rate is a very desirable way to improve process control: Using flow meters is more and more common, Keeping the pressure constant is another way
A constant flow rate can help to eliminate the cold flow that seems to come and go without explanation
The flow rate is determined by the smallest opening in the supply line - this is usually the quick connect fitting
Water (or oil) manifolds affect the flow rate if they are not carefully designed - there often is more output area than input area – Then which line gets the most flow?
Adjustment valves should be easy to see, easy to use, and have large openings for good flow
The water pressure at each machine should be consistent, and not vary – Many plants should have new piping installed
Hot oil systems will often make a significant difference in the surface defect rate for two reasons: – It keeps the die hot during stoppages - the start up scrap is often a high percentage of the total scrap, (this is where hot oil can easily pay for itself) – It can add heat to the die as needed to get better surface conditions
Hot oil units cool about half as effectively as water, so the thermal design must account for this to get the cycle times desired – Use higher flow rates, move lines closer, make larger, etc.

Some things to consider: Do not place water lines around the outside edge of the cavities (cool the cold areas); Give priority to cooling/heating lines, even if this means moving ejector pins or other changes; Do not use the same line to control temperatures in both a hot area and a cold area; Depth of the line is critical, set depths carefully; Size of line must match the flow rate; Treat water because deposits of only .005 cut heat transfer by about 40%
Another important control for the die temperature is the cycle time.
The die temperature at any given time is the direct result of the number of pounds of metal that went through the die in the last one to two hours.
A consistent cycle time is one of the most important factors in good defect control
The cycle time should be measured and displayed to the operator or technician in some way to get good control
Die temperature changes slowly, which can cause some delayed effects, and perhaps some confusion
Example: A change that adds nozzles to the spray manifold, and shortens the spray time with even more cooling than before, and also shortens the cycle time
There will be two effects, short and long term. The short term from the increase in spray cooling, the long term from the change in cycle time
Increasing the cooling from spray will reduce the die temperature quickly (short term)
Reducing the cycle time will increase the die temperature (long term)
Summary of correcting surface defects with die temperature: Measure die temperature to know where to change and how much; Establish temperature goals for minimum defects; Increase die temperature in the defect area by: Reducing spray, Reducing water flow rate, Adding overflows, Increase overall die temperature by: Reducing cycle time, Increasing hot oil temperature and flow rate
Summary (cont.): Use good spray practices and keep consistent, Use good computer aided thermal analysis for cooling/heating line design, Measure flow rates and control, Use good engineering to develop good quality water at consistent pressures, Minimize start up scrap and marginal production situations with die pre-heating; Keep die hot during short stops
(Thanks to All About Metallurgy for posting this PDF. We'll cover other aspects of die casting defect control from the course in upcoming blog posts)
(If you liked this article you might also like this post on, "Die Casting Defects")
Comments