Die Casting Porosity Causes and Solutions - Part 4
- Hill and Griffith
- May 2, 2018
- 5 min read
By Tim Cowell, Hill and Griffith Company, Technical Director
Shrink Porosity (Temperature) Note that the temperatures that affect the location of shrink die casting porosity are inside the casting itself. The die temperatures will influence the internal casting temperature, but they are not always effective in controlling it completely. Shrink porosity in a heavy section will be harder to move, shrink porosity in a thin section will be relatively easy to move. Complex shapes may respond different than you think.

Since the location of shrink porosity is also the hottest spot in that section of the casting, it is usually in the center of a heavy section. This hot spot location can be controlled to some extent by die temperature. The hot spot can often be moved by changing the die temperature - but this doesn’t reduce the porosity much - it just moves it.

An even casting temperature will cause the porosity to spread out, and to be roughly on the center line (the last point to solidify). Note that the center line is the last point to solidify only if the die temperatures are close to the same. Temperature differences between die halves can move the location.


It will move the porosity or spread it out - not necessarily reduce it - controlling porosity with die temperature is possible only on some castings. The shrink porosity location is determined by the temperature difference between areas in the casting - the hot and the cold spots are the things that determine the location of the porosity. Watch temperature difference between die halves. Remember, you can heat up the cold spot as well as cool the hot spot.
The other tool to fight shrink porosity is metal pressure. This is called the high pressure process. One of the primary reasons die casting machines use pressure is to reduce shrink porosity. The pressure can fill some of the voids as they develop, but timing and temperature are critical and very difficult to control.
Shrink Porosity (Pressure) The intensifier systems used with die casting machines are there to add pressure during solidification, resulting in the reduction of shrink porosity. Timing is critical: the porosity is not there when the metal is liquid, so pressure at that time doesn’t help (it will only add to flashing). After the casting is solid, the pressure obviously will not help. Therefore, the only time pressure can be used to feed more metal into the developing porosity holes is during solidification.

The most common die casting alloys have a freezing range - which means they go through a semi solid stage as they solidify. It is during this semi solid stage that we can add pressure and reduce shrinkage porosity by filling some voids as they are forming. Pure metals and some alloys called eutectic alloys solidify the way water does - that is the material goes directly from a liquid state to solid state at a single temperature - in this case there is no semi solid stage.

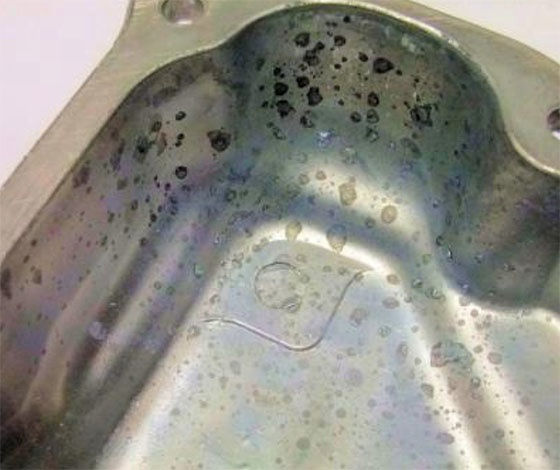
Some typical freezing ranges for the most common die casting alloys would be as follows:
380 aluminum 80 deg F
384 aluminum 120 deg F
413 aluminum 15 deg F
AZ91D magnesium 230 deg F
Zamak 3 zinc 10 deg F
Using pressure to fill the emerging shrinkage voids during this semi solid stage is a key factor in controlling shrinkage porosity. Several key control elements important in the use of pressure are:
The casting configuration, especially between the gate and the point of interest (thin walls?)
The amount of metal pressure available at the end of the plunger strode - the packing pressure
The intensified metal pressure
The rise time
The die temperature
The gate freeze time
The injection temperature
Casting configuration is the most important - it goes along with gate placement - of most importance is wall thickness and consistent shape. The metal pressures are important - both the pressure at the end of the stroke (called static metal pressure) and the intensified pressure. For heavy sections and large castings, the intensified pressure becomes most important - for thin walls and smaller parts, the static metal pressure is most important.
Typical values for minimum pressures would be:
Aluminum - Static 3,000 psi - Intensified 8,000 psi
Zinc - Static 2,000 psi - Intensified NA
Magnesium - Static 3,000 psi - Intensified 8,000 psi
These should be regarded as minimum for good casting quality internally - lower pressures are sometimes used when the internal quality is not that critical. For heavier section castings, some die casters use 10,000 psi as the minimum intensifier pressure.
The static and the intensified metal pressures should be checked in the design phase - if shrink porosity in a heavy section is a major concern, then a primary consideration in the process is the static pressure. When these minimums are used, they will determine the plunger size selected. Some castings run at lower pressures, small four slide zinc, for example, may run at 1500 psi or even less mostly because the shrink porosity is not as big of a problem as flash. Magnesium solidifies so fast that it is hard to operate the intensifier fast enough to make a difference.

Another big operation factor is trying to run with small biscuits - cavity pressure decreases very rapidly once the biscuit reaches a certain minimum. This minimum varies with the size of the shot sleeve, the metal temperature, the fill time and other factors. Below this minimum, the internal soundness of the casting will deteriorate very rapidly, even a being a little below the critical will greatly increase shrink porosity. The following graph shows some approximate results and illustrates the idea.

It is critical to monitor and control the factors controlling static metal pressure.
1. Check the process design for the proper selection of conditions to get the appropriate metal pressure, both static pressure and intensified pressure.
Plunger size
Hydraulic pressure settings
Intensifier pressure settings
2. Sleeve and plunger
Condition is very important for cold chamber, check lubrication, sleeve condition, tip condition, especially when there are intermittent shrink porosity problems.
3. Use a monitor system to check the many factors in the pressure trace at the end of the shot 4. Also check design factors, such as tip to sleeve clearances, cooling on the die end of the sleeve and other similar things
5. The nitrogen pre-charge will also cause the pressure at the end of the shot (static pressure) to trail off, and the casting will not get the “packing” pressure it needs to reduce shrinkage porosity
6. Check biscuit thickness for consistency and the appropriate value
Die Casting Process NADCA News:
Comments