Environmentally Friendly Sodium Silicate Binders
- Hill and Griffith
- Nov 7, 2017
- 5 min read
Corosil (Silicate Products) - Application to Aluminum Castings Sodium Silicate based products are one of the most environmentally friendly products that can be used in a core room.
The Indianapolis Manufacturing Facility has an excellent product line of Sodium Silicate Binders (Corosil and COBond). There have always been problems associated with the application of sodium silicate binders. The principal problem is in their inability to "shakeout" of a casting. The term "shakeout" applies to the ability or inability to remove the bonded sand from the solidified casting. As everyone would appreciate, if a foundry cannot remove the sand from the casting easily their costs of producing the casting would increase. In comparison, the less environmentally friendly processes do not have the severe difficulty of "shakeout".
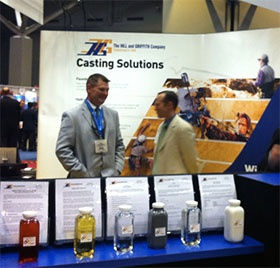
The advantage to the application of these binders when Aluminum Castings are produced is the fact that they are poured at a lower temperature than is Grey or Ductile Iron. Therefore, the Sodium Silicate Binders does not go through the "glass transition" (does not get as rigid). The result is that the "shakeout" is better. It is important to note that the problem does not go away, it is only reduced. Since the industry is headed towards the increase use of Aluminum Castings in the next century, our Corosil/COBond Products will benefit from this change in metal type.
Sodium Silicate Binders for Green Sand Metalcasting Foundry
Hill and Griffith Sodium Silicate Binders are formulated with water based solutions of Sodium Silicates and collapsibility agents. These binders are available in various percentages of carbonaceous materials as well as silica to soda ratios for varied or specific applications. The sand and silicate mixture is hardened by gassing with carbon dioxide (CO2). Molds or cores produced with Silicate binders result in castings with minimal veining, scabbing and penetration. Due to lack of mold wall movement, dimensional accuracy may be improved over some other casting processes.
Features
No Pollution Problems
No Need For Heat Curing
Odorless
No Organic Solvents
Good Bench Life When Protected From Drying Out
Excellent Flowability
Typical Product Data
| Ratio | Density | Viscosity (cps) | Organic Content |
Corosil GL | 2.58 | 12.66 | 1480 | 10.0 |
Corosil GN | 2.40 | 12.42 | 760 | 17.0 |
Corosil GR | 2.40 | 12.32 | 260 | 5.0 |
Corosil GU | 2.40 | 13.00 | 1110 | 0.0 |
Corosil GX | 2.40 | 12.32 | 375 | 5.0 |
General Information:
CoBond binder is a solution of sodium silicates that can be hardened on sand by a reaction with carbon dioxide. The curing process is quick and requires no heat. Therefore production rates are higher with a minimum of energy expenditure. There are no pollution problems with CoBond binder during mixing, gassing, casting, or shakeout because both the CoBond binder and carbon dioxide are odorless. CoBond binder contains no solvents and because it is nitrogen free it is suitable for steel castings. CoBond binder is characterized by the silica (SiO2) and soda (Na2O) ratio, specific gravity and viscosity. The specific gravity and viscosity determine the flowability of the sand mix while the silica (SiO2) to soda (Na2O) ratio determines the rate of cure and the strength properties of the sand. CoBond binder is supplied with silica (SiO2) to soda (Na2O) ratios from 2.00 to 2.58. In some CoBond binders, organic additives have been added to improve collapsibility. Practice indicates that the higher the organic content the better the collapsibility.
Curing Reaction:
When a sodium silicate solution is mixed on sand and then cured with CO2, complex chemical and physical changes occur that contribute to the hardening of the core or mold. The bonding phase that holds the sand together consists of (1) precipitated silica gel formed as a result of the reaction between CO2 and sodium hydroxide and the accompanying pH change and (2) dehydrated sodium silicate formed by removal of water as air passes through the sand.
The strength of a CO2 silicate cured core or mold depends primarily on the amount of the silica gel that is formed. Gassing parameters (pressure, flow-rate, CO2 concentration, gas time) are important in controlling strength. The most efficient use of CO2, is obtained by using low flow rates and reduced concentrations of CO2. This ensures that the CO2 remains in contact with the binder long enough to start curing, rather than being blown through quickly and at such high concentrations that much of it is wasted. It is more important to control flow rate than gassing pressure to obtain efficient CO2 use, which is typically 1.5% based on silicate.
If the maximum storage life is needed for a core or mold made with CoBond binder, then the minimum amount of gas needed to get acceptable strengths out of the box should be used. As the core of mold sits in the air, the binder will continue to cure and the strength will build up over a period of several days. If high strengths are needed only in the early stages of cure and storage time, then more gas should be used in the early stages of initial strengths. Cores or molds can actually over cure when stored. Low strengths at pouring can give improved collapsibility.
Handling Suggestions:
Nearly all types of foundry sands can be bonded with CoBond binder. Usually silica, lake, and bank sands of 45-130 grain fineness are used. Other sand types, as well as reclaimed sand, can be used providing they are not highly acidic. The moisture content of the sand should be less than 0.5% and the sand temperature between 55o - 95o F. (Hot sand shortens bench life and cold sands reduce flowability).
Use Levels:
For sand of grain fineness 30 - 50 the recommended binder level is 2 - 4 %. For sands of grain fineness number 50 - 80 the recommended binder level is 3 - 5 %. For sands of grain fineness number 80 - 160 the recommended binder level is 4 - 6 %.
Additives:
Kaolin, ball clay, fire clay or calcined alumina can be added at 1 - 2 % based on sand to increase hot strength. Seacoal at 3 - 5 %, iron oxide at 2 - 3 %, or pitch at 1 - 2 % will improve collapsibility. Any dry additive should be added to the sand before the CoBond
Mixing Equipment:
A mulling type mixing process is recommended. Mixing should be thorough but not too long. A total mixing time of 3 - 4 minutes is usually adequate. Short mixing times prevent heat build up and loss of water by evaporation. All mixes should be covered to prevent loss of water by evaporation.
Gassing:
The curing of a sodium silicate solution mixed with sand is the result of complex changes that contribute to the hardening of the core or mold. Usually the CO2 flow rate is 1 - 5 % based on silicate. Use a dry CO2 as water is detrimental to gassing speed and overall strengths. Phenolphthalein, at a level of 0.75 % based on sand, may be used as an indicator. The sand will appear red and areas that have been adequately gassed will become colorless; therefore, any red areas would require further gassing to start the curing reaction.
Coatings:
Water based coatings should not be used with CoBond bonded sand because the binder will dissolve in water and the core will soften. For best results, use either alcohol or chlorinated based washes.
Storage:
All CoBond and Corosil products should be protected from freezing. However, should freezing occur, the CoBond product may be restored to usable form by allowing the contents to come to room temperature and thoroughly mixing the product. For best results, store between 55 - 95o F. Containers should be closed as completely as possible to prevent exposure to CO2 and to prevent changes in viscosity due to water evaporation.
Safety Precautions:
In general, Cobond binder is manufactured using components having low order of toxicity. Fluid or vapor in the eyes or on the skin may cause transitory irritation that disappears within 24 hours. Flushing the eyes with flowing water and washing the skin with soap and water will usually prevent discomfort. If irritation persists, consult a physician. Material Safety Data Sheets outlining known hazards and safety precautions associated with the product are available and should be used accordingly.
Comments